
Festo introduces new solution for automating EV battery manufacturing
This development is part of a broader initiative by the company to innovate across the entire battery lifecycle.
October 3, 2024 | By MRO Magazine
Festo has announced it has created a new solution for high throughput dry-room electrode assembly of electric vehicle (EV) batteries.
This development is part of a broader initiative by the company to innovate across the entire battery lifecycle. In 2022, the Festo electric mobility initiative demonstrated an automated degassing cell. In 2023, the company developed an automated chemical processing solution for recycling the valuable materials incorporated within EV batteries.
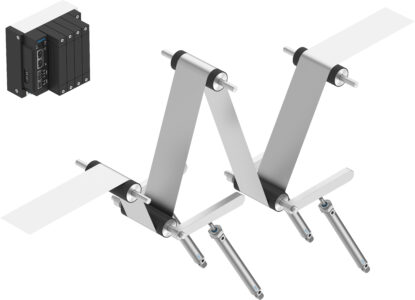
The world’s first proportional valve terminal, the Festo VTEP, top left, is ideal for the web control of battery foils.
The latest technology focuses on the production of electrodes, specifically the unrolling, cutting, aligning, and layering of anodes and cathodes. A key component of this process is the Festo VTEP, the first high-precision proportional valve terminal available on the market, which maintains roll tension—a crucial factor for battery quality. This valve system is reported to offer cost savings compared to traditional electric automation methods.
VTEP is the latest Controlled Pneumatics solution from Festo. Controlled Pneumatics is the next stage in the evolution of pneumatic solutions for the 21st century. Controlled Pneumatics solutions combine high-speed, long-life, and energy-efficient piezo-electric valve cartridges with sensors and control algorithms into a single smart unit.
With VTEP, users set performance parameters per valve channel and the proportional pressure valves provide closed-loop control to those presets. Valves deliver highly dynamic response and precise pressure control to achieve “target reached” status for each channel, which equates to the motion complete function in electric drive technology. Sustaining the target setting makes the VTEP terminal ideal for maintaining roll tension in automated dry room electrode production.
Festo says its components for dry room applications are designed to be copper and zinc free, aligning with industry best practices. The company offers these environmentally friendly options across a range of product families, identifiable by an “F1A” designation in their model numbers.
Festo Didactic, the educational division of Festo, is addressing the skills gap in EV and semiconductor manufacturing by offering online training programs and on-site customized training to help establish and maintain apprenticeship programs.
Print this page